The flap carton production process - from raw material to finished product
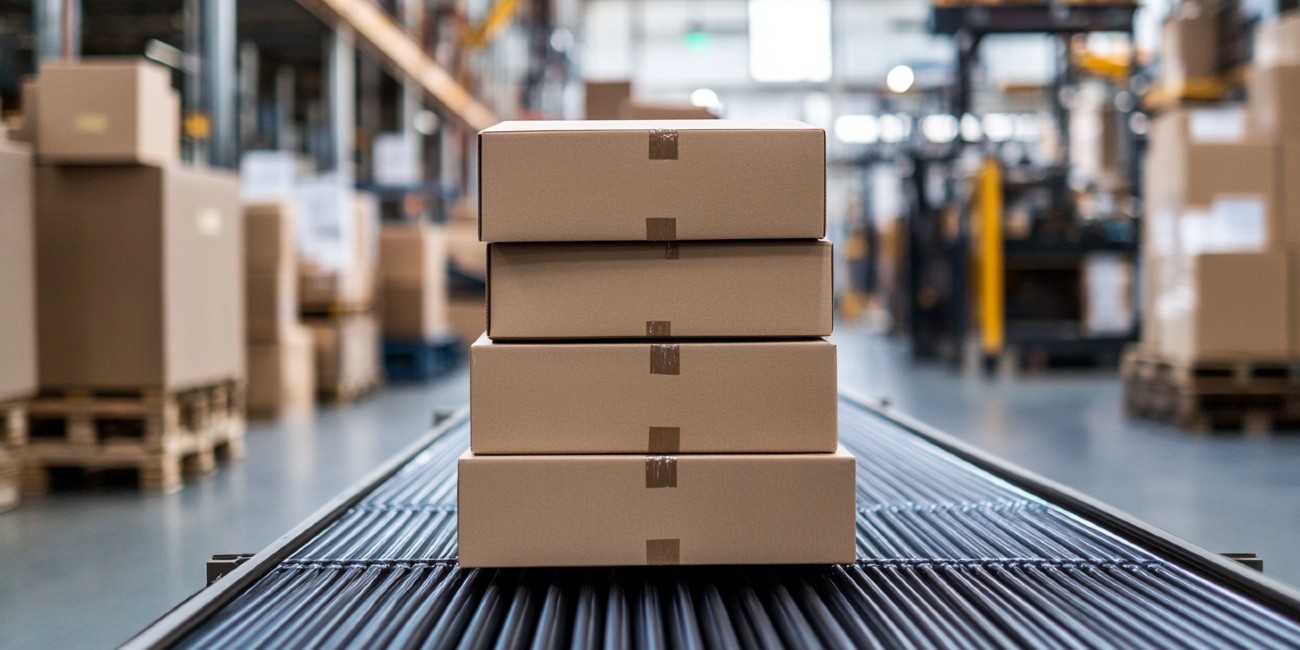
Contents:
- The Production Process of Flap Boxes – from Raw Material to Finished Product
- Key Points
- The Importance of Raw Materials – How Corrugated Board Is Made
- What Is Corrugated Board?
- Corrugated Board Has… Layers
- How to Choose the Right Corrugated Board for the Product You Want to Ship
- Summary
- FAQs – Frequently Asked Questions
The Production Process of Flap Boxes – from Raw Material to Finished Product
Flap boxes are part of our daily life – from moving house, to storage, to transporting all kinds of products. From simple raw materials such as paper and corrugated board, we get sturdy, eco-friendly packaging that effectively protects its contents even under difficult transport conditions. In this article, we’ll take a closer look at how these durable and versatile solutions are made, serving us at every stage of the logistics process.
Key Points
- The flute type in corrugated board provides different levels of compression and impact resistance, allowing the boxes to be tailored to the nature of the goods being transported.
- Multi-layer corrugated board provides exceptional strength and shock resistance, which is crucial for shipping heavy and delicate items.
- Choosing the right board type for a given product ensures safety and proper protection during shipping or storage.
The Importance of Raw Materials – How Corrugated Board Is Made
Corrugated board is the key material used to produce flap boxes. It is derived from resources such as virgin paper or recycled paper, making reuse and recycling possible – an eco-friendly solution we discuss in detail in Ecological Advantages of Flap Boxes – Recycling and Sustainable Solutions.
The process of making corrugated board begins with processing the raw material, carried out mainly by two methods: wet and dry. The table below describes the differences between these methods and their main characteristics.
Fig. Table comparing the dry and wet processes of making paper (board).
Criterion | Wet Method | Dry Method |
---|---|---|
Production Process | Under the wet method, cellulose is first shredded and mixed with water, forming a paper pulp that is then shaped and dried. | With the dry method, materials like wood fiber are processed almost without water using mechanical procedures to create paper. |
Efficiency | Less efficient; it is more time-consuming due to the need for water and more stages. | Highly efficient; production is faster because it uses dry pulp and more advanced techniques. |
Box Quality | Higher quality, especially where greater strength and flexibility are required. | Lower quality, less flexible and durable, but sufficient for mass-market applications. |
Technologies & Machinery | Requires more complex technologies, e.g. machines for shaping and drying the pulp (paper mills). | Uses paper mills and other mechanical methods to efficiently turn raw materials into paper. |
Water Consumption | Needs a large volume of water for fiber hydration and forming steps. | Minimal water consumption, as the process occurs mostly “dry.” |
Production Cost | Higher cost, due to a more complex procedure and greater use of energy and water. | Lower cost, as the process is more efficient and uses fewer resources. |
Solid board produced by the wet method is often used for gift boxes, luxury packaging, or packaging for books and other items requiring a polished finish. However, it is not best suited for reliably transporting objects, due to its relatively lower durability.
In flap box production, on the other hand, the dry method is most common, since it creates corrugated board that is then used to make light but strong flap boxes – perfect for shipping and storing a wide range of items.
What Is Corrugated Board?
Corrugated board consists of several layers of paper, one of which is fluted while the remaining layers are flat. During production, one paper layer passes through specialized rollers to create the characteristic “flutes.” These layers are then glued together to form a material that is both strong and flexible.
We classify corrugated board by flute type, which differs in “thickness and strength.” Here are some examples:
- Flute A – approx. 4–5 mm. One of the thicker flutes, offering high compression and impact resistance.
- Flute B – approx. 2.5–3 mm. A medium flute, commonly used where a good printing surface is needed.
- Flute C – approx. 3.5–4.0 mm. Frequently chosen for boards needing strong compression resistance.
- Flute E – approx. 1.1–1.8 mm. A thinner flute with an outstanding surface for printing.
- Flute F – approx. 0.6–1.0 mm. Even thinner, for very fine cardboard requiring high printing detail.
Flute N – a relatively new type of microflute, about 0.5 mm high, used in extra-light corrugated board.
It’s important to note that flute parameters can be modified to achieve the exact strength and flexibility needed by a given product.
This way, we can create flap boxes that effectively protect goods from damage. Common combinations include:
- BC – (B flute & C flute) – Combines medium flutes that offer good compression and shock resistance along with a decent surface for printing. Used for medium-sized items like electronics or small household appliances.
- AB – (A & B flute) – The thicker A flute combined with the thinner B flute yields high dent-resistance and good print quality. Often used for packaging fragile objects needing strong protection.
- AC – (A & C flute) – Large A flute plus a C flute, providing high compression resistance and robust mechanical strength. Ideal for shipping heavier or more delicate goods.
- BCB – (B, C, B flute) – Two layers of B flute around a C flute for exceptional resistance to pressure and impacts. Applied in large, heavy product packaging (e.g. household appliances).
- EB – (E & B flute) – E- and B-flute combined create a thinner yet strong board that prints well. Used for lighter retail packaging (consumer items).
- EC – (E & C flute) – Merges E and C flutes for a lightweight board with decent compression resistance and a suitable printing surface, commonly found in light retail packaging such as electronics.
- AAC – (A, A & C flute) – Two layers of A flute plus a C flute ensure high protection against mechanical damage and a strong load-bearing capacity. Used for transport packaging of heavy or fragile products.
Corrugated Board Has… Layers
Corrugated board is also categorized by the number of layers it contains. The following table explains these differences:
Fig. Table showing the “composition” of corrugated board depending on the number of layers.
Type of Board | Layers | Use |
---|---|---|
2-Ply Corrugated Board | 1. Liner (top layer) 2. Fluted (corrugated) layer |
Mainly used for shipping packages, in warehouses, or for simpler transport packaging. |
3-Ply Corrugated Board | 1. Liner (top) 2. Fluted layer 3. Liner (bottom) |
The most commonly used in the packaging industry. Flute variations (B, C, E) of different heights affect strength and appearance. |
5-Ply Corrugated Board | 1. Liner (top) 2. Liner (paper layer) 3. Fluted layer 4. Fluted layer 5. Liner (bottom) |
Used for transporting large and heavy products. Combinations like EB or BC provide high mechanical damage resistance. |
There is also 7-ply corrugated board consisting of three fluted layers plus four liner layers, providing very high mechanical resistance for demanding packaging, e.g. for very heavy or extremely delicate products.
How to Choose the Right Corrugated Board for the Product You Want to Ship
Deciding which corrugated board type is appropriate depends on several factors: the nature of the product, its weight, fragility, and required level of protection. Below are the main aspects to keep in mind:
- Weight and Dimensions of the Product – Heavier and bigger items, such as household appliances or furniture, need stronger corrugated board. A 5-ply board (e.g. BC or BCB flutes) offers reliable resistance to dents and mechanical damage. Lighter goods (electronics, consumer products) often do fine with a 3- or 4-ply E flute, providing decent compression strength with less weight.
- Product Type and Fragility – Highly fragile products (electronics, glass, pharmaceuticals) require enhanced protection. A board with multiple layers, e.g. 7-ply, maximizes shock absorption. If the product is especially prone to scratches, a smoother outer surface, such as E flute, may be important.
- Transport Requirements – The packaging must withstand shipping conditions: temperature changes, humidity, and vibration, especially on long hauls or international routes. In such cases, a 5-ply board is better for extra defense against damage and harsh conditions.
So the right board depends on the specific needs of the product. A well-chosen material ensures security in transit and may double as a marketing component, highlighting the quality and aesthetics of the package.
If you’re still uncertain or have doubts about which board type to use, we’ll be glad to help! BoxMarket offers a broad selection of flap boxes, making it easy to find the optimal solution for your requirements. Our specialists will gladly advise you about the proper strength, cushioning, or printing surface. Contact us, and we’ll answer all your questions about shipping, packing, and choosing the right filler, ensuring total satisfaction with your purchase.
Summary
Flap Boxes are widely used across different industries for storing, transporting, and packaging goods. Because they’re produced from corrugated board, these boxes are strong enough to protect their contents even under challenging transport conditions. Their production process begins with raw material treatment, and picking the right corrugated board depends on the weight, fragility, and nature of what’s being shipped. Flute type and the number of layers determine the board’s resistance, so you can always opt for packaging that reliably shields its contents, whether electronics or large household appliances.
The diagram below illustrates the entire flap box production process:
FAQs – Frequently Asked Questions
- Are flap boxes suitable for packing fragile items?
Yes, flap boxes are excellent for delicate goods. For especially sensitive objects, choose thicker board or a box with added cushioning to provide maximum protection against shocks and damage. Boxmarket’s range includes 3- and 5-ply flap boxes – ideal for fragile items. - Can flap boxes be used for international shipping?
Absolutely. Flap boxes are well suited to long-distance transport, provided you choose a board type that matches requirements like temperature changes, moisture, and potential impacts during shipping. - Are flap boxes easy to fold?
Yes, flap boxes are designed for quick, easy assembly, featuring pre-creased edges and fold lines that help you shape them with minimal effort. - What else can flap boxes be used for?
Flap boxes are also used for storage, archiving, and moving house. Thanks to their versatility, as well as ease of folding and storing, they’re popular not just in transport but also for keeping things organized in offices or at home.