How is the durability of flapping cardboards tested?
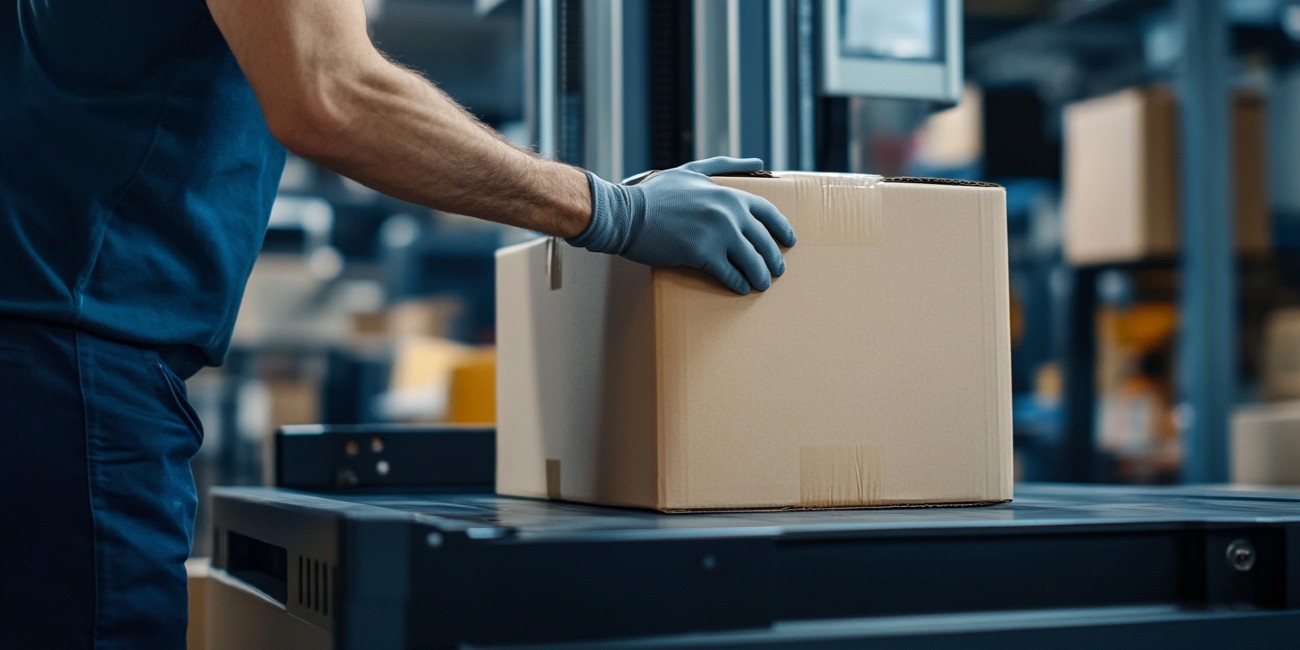
Contents:
Flap boxes made of corrugated cardboard are among the most frequently used types of packaging, especially in logistics and warehousing. Due to their extensive range of applications, it is essential to test their strength properties. The testing process is carried out in several key stages, and the methods used are adapted to the specific characteristics of the industry in which the cardboard will be used. How does it look in practice?
Key Points
- Testing the durability of flap boxes ensures their appropriate quality and safe transport.
- Tests such as BCT, Mullen Burst, and Cobb Test assess a box’s resistance to compression, puncture, and moisture.
- Compliance with international quality standards is essential for companies exporting products.
Why Is Testing the Strength of Boxes Important?
In today’s world, almost every product must go through a series of rigorous tests before reaching the consumer. From toys and electronic devices to means of transport – everything undergoes thorough verification to ensure safety and quality. The same applies to flap boxes, which play a crucial role in logistics, storage, and transport.
Here are the main reasons why these tests are indispensable:
- Quality certification – Tests make it possible to award certifications confirming that the packaging meets specific standards. As a result, only products from responsible manufacturers reach the market.
- Consumer protection – Sturdy boxes protect goods such as food, medicine, or delicate devices from damage, directly influencing user safety.
- Prevention of losses and accidents – High durability of flap boxes reduces the risk of product destruction during transport, and in the case of hazardous materials, helps prevent health- or environment-threatening incidents.
- Building trust – A manufacturer who invests in testing shows a commitment to quality and a concern for customer needs. Certified boxes instill more trust and reduce the number of complaints.
- Environmental responsibility – Durable and thoroughly tested boxes are more efficient and can be used longer, thus reducing waste.
In short, testing is more than just a technical check – it’s about quality, safety, and responsibility, which translate into better products and greater customer confidence.
The Most Common Strength Tests for Flap Boxes
- Box Compression Test (BCT) is one of the most important strength tests, measuring a box’s ability to endure loads under storage and transport conditions. The main purpose of this test is to evaluate how the box reacts to even pressure applied to its surface. The box is placed between two plates of a testing machine, which gradually compress it until the box is crushed or deformed.
The BCT helps determine how much weight the box can withstand before it starts deforming or suffering damage. This is crucial because in practice boxes are often subjected to high pressure during storage in warehouses, transport, or other logistical operations. The test shows whether the packaging material is strong enough to protect the contents of the package.
BCT results are expressed in units of force, most commonly in Newtons, enabling precise determination of how much pressure the box can handle. Based on the test results, one can also determine which storage, transport, and handling conditions are safe for a given box. Furthermore, the data helps packaging designers and manufacturers select appropriate materials for box production, ensuring durability throughout the product’s lifecycle. - Mullen Burst Test is a strength test that measures a box’s resistance to punctures. Its main goal is to specify how much force is needed to pierce the box. This test uses a device equipped with a rubber membrane that gradually exerts pressure on a sample of the cardboard until it tears or punctures.
The test assesses how well the box withstands pressure and whether it is resistant to damage caused by impacts or sharp edges of other objects during transport. Specifically, this test is important in industries where goods may be stored or transported in conditions that expose the packaging to impacts or contact with sharp objects (for example, in the food, pharmaceutical, or electronics sectors).
Based on the test results, packaging manufacturers can adjust the thickness of the board, its composition, or the production process to ensure adequate protection of goods from accidental damage during transport and storage. - Cobb Test is a moisture absorption test used to assess the ability of corrugated board (
the material used for flap boxes
) to absorb water. Since cardboard is a material that can absorb moisture, the aim of this test is to determine how much water the material can take up over a certain period.
Boxes used in warehouses , outdoors, or in transport may be exposed to moisture and rain. The Cobb Test determines whether the material is sufficiently resistant to maintain its protective properties even in challenging weather conditions.
But that’s not all. The results also allow manufacturers to modify the composition of the packaging material to improve its moisture resistance, adapting it to specific transport or storage requirements.
Other Strength Tests for Flap Boxes
Of course, there are many other tests that affect the assessment of flap boxes’ strength, and fully discussing them would require more space than we can devote to a single article. Nonetheless, it’s worth noting that these methods also play a key role:
- Adhesion Test – checks how well the joints in the box withstand various operating conditions. It tests whether the adhesive used for bonding the cardboard maintains its properties when exposed to moisture, temperature changes, or other environmental conditions. This is particularly important in transporting goods that may be exposed to varying environmental factors.
- ECT (Edge Crush Test) – measures the cardboard’s strength under vertical compression to evaluate its resistance to forces exerted on the box edges. This test determines how well the box can handle side loads that may occur during transport or when boxes are stacked.
- Vibration Test – checks the box’s resistance to vibrations encountered during transport (e.g. in road, rail, or maritime shipping). It aims to ensure that neither the box nor its contents will be damaged by vibrations that can occur over long-distance transport.
International Quality Standards for Flap Boxes – Meeting Requirements
To conduct effective strength tests for flap boxes, specialized machines are used in labs to precisely measure different packaging properties. These devices are carefully calibrated according to relevant standards to guarantee high accuracy of results and enable an objective assessment of a box’s strength.
Flap boxes, being one of the most commonly used packaging types, must comply with certain international standards that define quality guidelines and testing methodologies. Below are the most important ones:
- ISO 12048 – an international standard that specifies methods for testing compression strength, i.e., the BCT.
- ASTM D642 – a U.S. standard regulating how box compression tests are carried out, determining a box’s performance under load during storage or transport.
- ISTA 1A – a packaging test procedure focusing on resistance to transport conditions, especially for boxes used in international logistics.
- ISO 18601 – relates to general requirements for packaging and its environmental impact. It outlines guidelines to minimize the negative environmental footprint of packaging, which can be crucial for flap boxes widely adopted in eco-friendly packaging production.
Compliance with these and many other standards is essential for companies exporting their products, since it ensures adherence to international regulations and boosts trust in the quality of the offered packaging.
Summary
Strength testing of flap boxes is a key process ensuring they meet the required quality and safety standards during transport and storage.
When buying flap boxes from Boxmarket, you can rest assured that the products offered have undergone all necessary strength testing. Each box is meticulously checked for resistance to compression, punctures, moisture, and other external factors. Moreover, Boxmarket guarantees that the packaging it supplies complies with current international quality standards, backed by relevant certifications. This way, you have the certainty of choosing a product that effectively protects your goods, minimizing the risk of damage and complaints.
Testing consumer goods, particularly regarding safety and quality, began to be systematically introduced in the 19th century.
One example is the British Standards Institution (BSI), founded in 1901, which started setting standards for various consumer products, including those used in construction, electronics, and the automotive industry. The tests aimed to ensure that products met certain safety and quality requirements.
FAQs – Frequently Asked Questions
- Are box strength tests mandatory?
Yes, box strength tests are mandatory, particularly for products intended for export and required to meet international quality standards. Packaging certification ensures safety and compliance with regulations in different countries. - How long does a standard box strength test take?
The duration depends on the test type. For example, the Box Compression Test (BCT) can take only a few minutes, whereas a moisture absorption test (Cobb Test) may last several hours. The time varies according to the complexity and requirements of the specific test. - Does every box need to undergo strength testing?
No, not every single box is tested. In practice, representative samples from a production batch are tested. This approach yields reliable results that apply to the entire range of boxes. - What are the consequences of not conducting box strength tests?
Failure to carry out appropriate strength tests can lead to merchandise damage during transit, causing expenses for returns and warranty claims, and harming the company’s reputation. In extreme cases, inadequately designed boxes can pose health or safety risks, especially for hazardous or delicate materials.